How to Secure Cargo on Open-Deck Trailers
Securing a load on an open-deck trailer presents a unique set of challenges, with no walls to contain cargo. Those who secure the payload to the trailer’s structure (most often the driver) have to be knowledgeable about federal regulations, understand some basic laws of physics, and be familiar with the characteristics of the trailer they are hauling. If they don’t, it can result in the accumulation of CSA points, an out-of-service citation, or a catastrophic cargo securement failure.
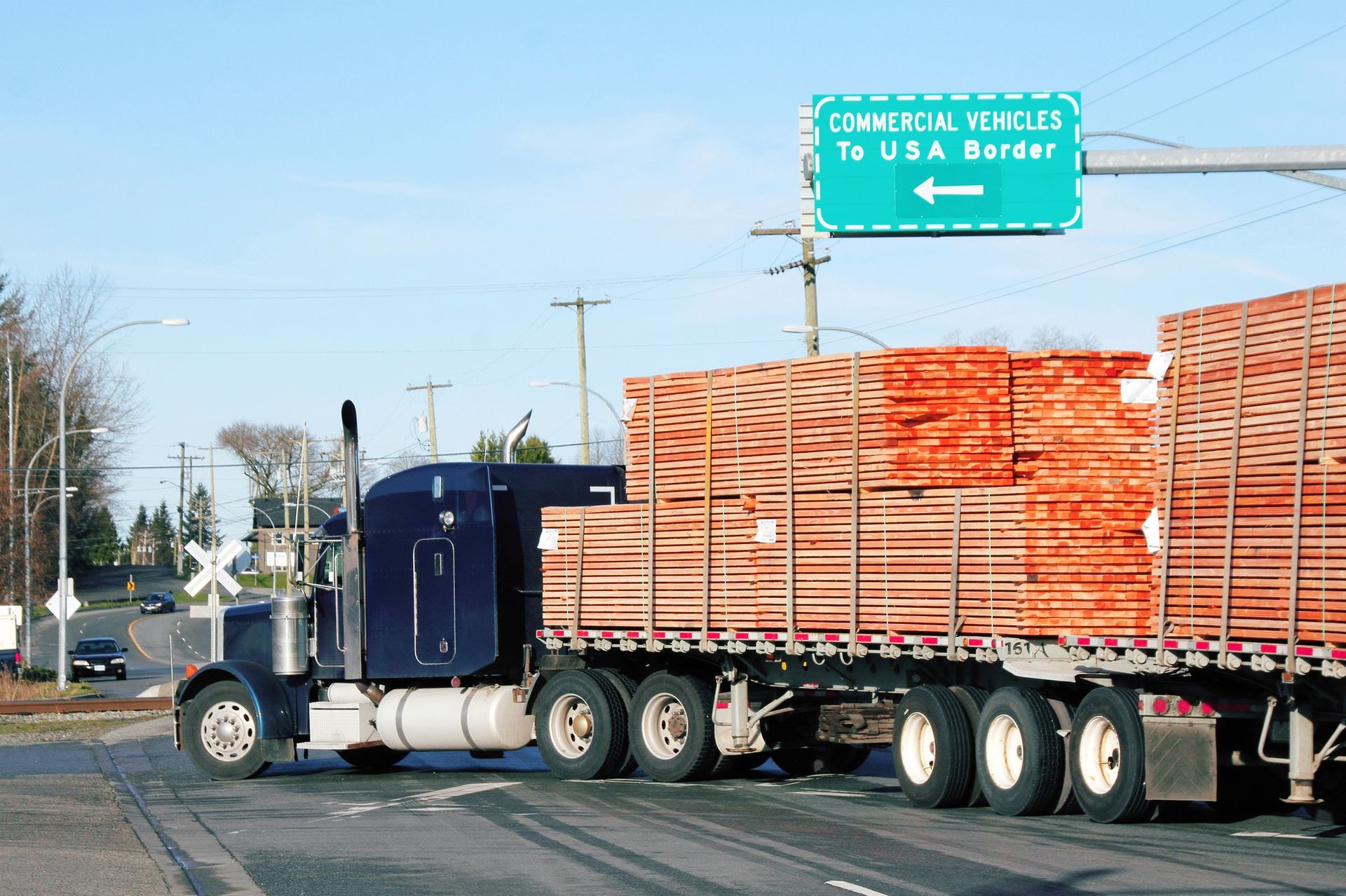
Cargo types can vary significantly, with materials such as lumber, metal coils, pipe, crushed vehicles, boulders, and everything in between. Heavy-haul drop deck and lowboy trailers may carry large, articulating equipment to and from off-highway worksites. Or oversize loads, like a 56-ton wind turbine nacelle, might be on the bill of lading.
Some fleets and drivers specialize in hauling a particular type of cargo and can become quite proficient at the process of securing it. Many others deal with significant variability, which can lead to trouble.
Know the Regulations
There is no substitute for a thorough understanding of federal regulations. In North America, the official regulations are governed by two key entities. In the United States, the Federal Motor Carrier Safety Administration establishes the regulations. In Canada, the regulations are set forth by the National Safety Code Standard 10 — Cargo Securement (NSC 10).
FMCSA’s Drivers Handbook on Cargo Securement classifies different commodities and stipulates the standards for proper securement of these specific load types:
- logs
- dressed lumber and similar building products
- metal coils
- paper rolls
- concrete pipe loaded crosswise on a platform vehicle
- intermodal containers
- automobiles, vans and light trucks
- heavy vehicles, equipment and machinery
- flattened or crushed vehicles
- roll-on/roll-off hook-lift containers
- large boulders.
FMCSA regulations are informed by standards published by The Web Sling and Tie Down Association (WSTDA) regarding recommended standard specification for load securement devices, including synthetic web tie-downs, winches used with web tie-downs, and load binders used with chain tie-downs. The WSTDA standards detail definitions, construction, testing procedures, and operating practices for tie-downs, winches, and load binders. The National Association of Chain Manufacturers writes the standards for steel chain used for load securement.
Do the Math
When moving, an open-deck trailer is a dynamic environment that exerts physical forces on the cargo it bears. As soon as a trailer begins to roll, the mechanical action and movement of the trailer is transferred to its cargo. In order to secure cargo to the deck of a trailer successfully, one must understand the basic forces at hand and how they can cause a payload to shift, tip, slide and otherwise become unstable.
The gravitational force equivalent, most commonly referred to as “g-force,” is the most important part of the equation, and it is represented as simply “g.” One g is basically equal to something’s weight here on earth. Knowing the weight of the cargo is necessary to understand performance criteria for the breaking strength and related working load limit (WLL) of tie-down assemblies (including chains, wire rope, steel strapping, synthetic webbing and cordage) and other attachments or fastening devices used to secure articles of cargo. All such devices are manufactured to include clearly marked information on WLL — and these must remain legible for tie-down assemblies to remain in service.
According to FMCSA regulations for performance criteria, cargo securement devices and systems must be capable of withstanding the following three forces, applied separately:
- 0.8 g (or 80% of the weight of the cargo) deceleration in the forward direction;
- 0.5 g (or 50% of the weight of the cargo) acceleration in the rearward direction; and
- 0.5 g (or 50% of the weight of the cargo) acceleration in a lateral direction.
Securement systems must provide a downward force equivalent to at least 20% of the weight of the article of cargo if the article is not fully contained within the structure of a vehicle.
WSTDA has established the design factor of tie-down straps as 3:1, or a WLL of 1/3 of the tie-down strap’s breaking strength. For chains, the design factor is 4:1 or a WLL of 1/4 of the chain’s breaking strength.
The combined ratings of all the straps or chains must equal at least half the load’s total weight. If the load is 40,000 pounds, the aggregate WLL of all the tie-downs together must equal at least 20,000 pounds.
Along with FMCSA guidelines, ensure that these four critical conditions are met:
- cargo should be fully contained and supported by the flatbed structure and should be restrained from any horizontal or vertical movement;
- cargo should be fully restrained from shifting or tipping over by the truck’s structure and blocking implements of adequate strength, and
- cargo should be completely immobilized by appropriately applied tie-downs so it can withstand the required g-forces in all directions.
Consideration should be given to the angle from the horizontal tie-down to its anchor point on the trailer, as this affects the downward pressure. The lower the angle, the less pressure and friction against the load. This may result in the need for additional tie-downs.
Often overlooked, the angle of a tie-down assembly can significantly decrease the amount of downward pressure exerted on a load, reducing friction between tiers of stacked cargo, and ultimately, against the deck. As an example, at a 30-degree angle, a tie-down may only be able to exert 50% of its effective downward pressure, which under certain circumstances may allow some cargo, including sheeted materials, to slide or become unstable.
The noted angle factors assume equal tension on all parts of the tie-down assembly, but in reality, tie-down tension varies from side-to-side due to friction on the cargo. So the effective downward pressure impact on actual load securement is compounded.
In all cases, chains and straps face limits on cuts, breaks and other defects as defined in a Defect Classification Table in the CVSA guidelines. Inspectors use the Out Of Service Guideline when examining a vehicle’s cargo securement. It’s wise to make chain and strap inspection a part of any cargo securement process.
Size Things Up
Load securement requires some planning and an assessment of the vehicle, the tie-down appropriate for a particular load, and the load itself. Good securement starts with a clean, safe and structurally sound trailer. It is also important to inspect and verify that the critical components of the vehicle involved in the securement are in good condition and are not weakened or corroded. Of particular importance are the deck structure and the anchor points for the tie-down.
The system or systems one chooses should depend on the characteristics of the load. Is it configured as one piece or as constituent pieces? Will it be prone to sliding? Does it have sharp corners that could cut through webbing? Does it have engineered anchor points that allow for “direct” securement attaching to the article, or nothing to attach to, requiring “indirect” securement that passes through, over or around the article? The cargo itself must also be strong enough to withstand the pressure of securement without becoming damaged.
In addition to traditional cargo securement and fastening devices such as binders, winches and hooks, there are a variety of tools that can be employed to enhance cargo securement effectiveness. Wood or rubber chocks may be added to promote stability. Corner protectors can be used to cover sharp edges that could cut webbing and to distribute downward force, avoiding edge-crushing damage to cargo such as shingles. Netting can be applied to unitize otherwise unstable cargo. Anti-slip mats can increase the coefficient of friction between the load and the load-bearing surface.
It’s Not Over Until It’s Over
Even if cargo is expertly secured at the outset, once it and the trailer are on the move, things can and will change. Per FMCSA 392.9, Inspection of Cargo, Cargo Securement Devices and Systems, drivers are required to inspect cargo before driving the vehicle and no more than 49.7 miles (80 kilometers) from where the cargo is loaded.
Periodic inspection of cargo securement devices and systems is mandatory when:
- There is a change of duty status for the driver, or
- The vehicle has been driven more than three hours, or
- The vehicle has been driven for 149.129 miles (240 kilometers).
Content Disclaimer: Due to the constantly changing nature of government regulations, it is impossible to guarantee the total and absolute accuracy of the material contained herein or presented. NorthAmerican Transportation Association (NTA) cannot and does not assume any responsibility for omissions, errors, misprinting or ambiguity contained. NTA shall not be held liable in any degree for any loss, damage or injury caused by any such omission, error, misprinting or ambiguity present. It is made available with the understanding that NTA is not engaged in rendering legal, accounting or other professional service. If legal advice or other expert service is required, the services of such a professional should be sought.